Product
Information
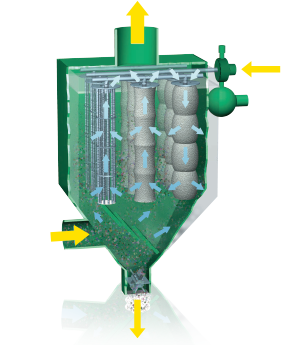
Baghouse Dust Collector
This product removes dust in the manufacturing process of cement, steel, mining, chemical, food, garbage incineration, and industrial waste treatment facilities. The product filters dust and debris generated inside cement plants, waste incineration plants, and other plants and releases clean air outside the facilities.
Long, rich experience and accumulated know-how
Since the production and delivery of the first Baghouse model in 1950, we have a wealth of experience in all fields, including cement, steel, mining, chemical, food, waste incineration, and industrial waste treatment facilities, both in Japan and overseas.
Providing the right model for the right situation
We can meet our customers’ needs with products for various applications, ranging from a high-performance, compact pulse type to a simple, trouble-free, low operational cost mechanical type.
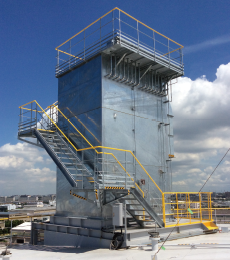
Baghouse Dust Collectors Introduction Video
Roles of Baghouse Dust Collector
A dust collector employing a dry filtration method using a baghouse, which collects dust in plants with high efficiency, has been improved to provide equipment suitable for all operating conditions.
Baghouse collect dust generated in
each manufacturing process.
Dust is removed from mining, refining, cement, chemical, steel, waste disposal, and manufacturing processes in diverse industries.
Protecting clean air inside and outside
the facilities.
The air is filtered by baghouses, separated into clean air and dust, and the clean air is discharged outside.
Recovering and reusing resources.
Our improved dust collection technology is effective in environmental protection and the recovery and reuse of resources.
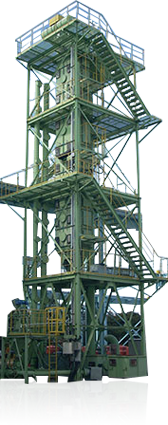

Types and Model Features of Baghouse Dust Collectors
Atmospheric backwash type
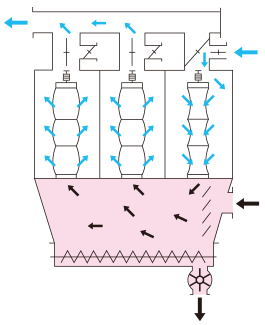
- The exhaust heat minimizes acid condensation caused by the inflow of backwash.
- No pulse valves are required, and there is no noise generation.
- Free of freezing trouble that tends to occur in cold regions.
- Fewer parts and low maintenance costs.
- Less damage during filter removal, resulting in longer filter life.
- A large volume of compressed air is not required, reducing running costs.
- Even with powders that have low specific gravity or do not agglomerate, there is no trouble with an increased pressure drop that may otherwise result from re-scattering after filter removal.
Pulse-jet type
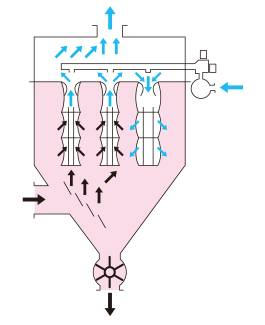
- The initial cost is lower than that of the atmospheric backwash type in the case of small and medium-sized equipment.
- Immediate removal of filter and less fluctuation in air flow rate.
- High-speed filtration is possible, and the size is more compact than the atmospheric backwash type.
- Less damage during filter removal and longer filter life.
- Filter replacement is performed outdoors, which is easier than that for the atmospheric backwash type.
TModel
Simple structure with atmospheric backwash
Filtration method: Internal filtration type,Filter cloth diameter: 170, 200, 292
Air flows naturally from the outer surface of the filter to the inner surface by opening and closing the exhaust back-pressure damper.
Displacement of the filter and the slight vibration of the spring attached to the filter top cause the air to flow out of the filter.
This model has a simple structure, low running costs, and excellent removal performance.
It is especially suitable for cold, hot, and humid areas where compressed air is not used or noise is a problem.
Special felt with surface treatment has recently been used for baghouse with a high dust concentration of 1,000 g/Nm³ or more.
LPModel
Large-size pulse-jet type
Filtration method: Internal filtration type,Pulse pressure: Low pressure less than 0.2 MPa,
Filter cloth diameter: 130
The filter length is as long as 6,000 mm. Therefore, it is used in relatively large pulse-type baghouse that are 1,000 m² or more. The baghouse requires less space for installation, and it has recently been widely used for municipal waste incinerators.
YPModel
Medium-size pulse jet type
Filtration method: External filtration type,Pulse pressure: High pressure less than 0.5 MPa,
Filter cloth diameter: 116, 165
Compressed air is injected through a nozzle attached to the top of the filter for dust removal.
Because of the external surface filtration, relatively high-speed filtration is possible. Therefore, the initial cost is low for the medium size (1,000 m² or less), and the equipment space is compact.
Also, because the system performs immediate dust removal, the filter can minimize fluctuations in pressure.
SPModel
Pulse-jet type with internal replacement of filter cloth
Filtration method: External filtration type,Pulse pressure: High pressure less than 0.5 MPa,
Filter cloth diameter: 116
The YP and LP types have a maintenance hole on top, and the filter is replaced from the outside by opening the maintenance hole. The SP type is designed to replace the filter inside. It is suitable for buildings with limited ceiling height and high-pressure-resistant applications.
Case example: Cement calcination plants
exhaust gas facilities
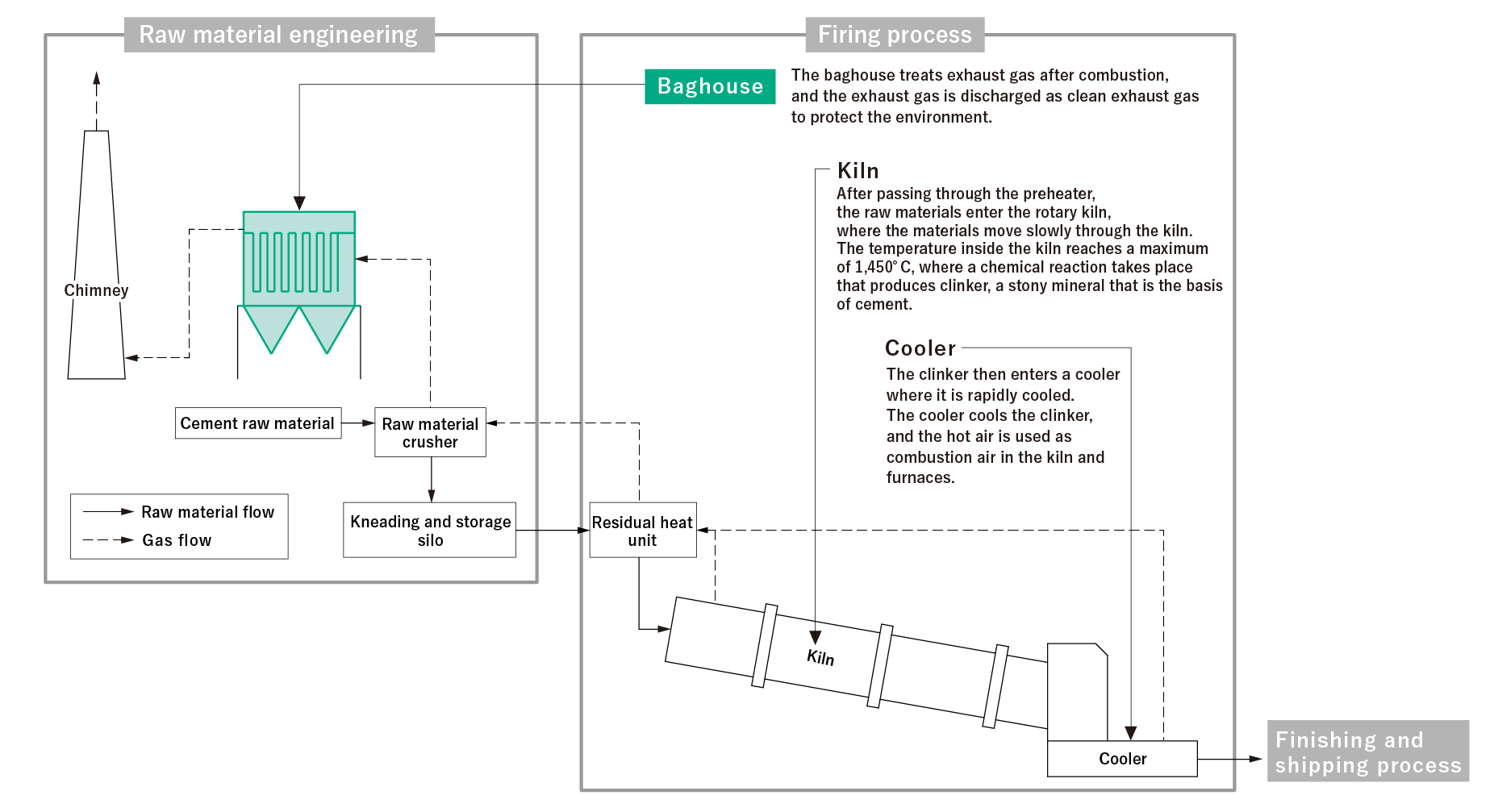